Kevlar, Kolfiber, Honeycomb,
etc:
BÅTBYGGARNAS NYA SUPERMATERIAL
E-glas, S-glas, Kevlar och kolfiber. En del av alla de
material som används för att bygga båtar. Vad har de för egenskaper, vad är det som
skiljer dem åt?
Båtbyggaren Nisse Luoma reder ut begreppen och förklarar sammanhangen. Han har själv
stor erfarenhet av att arbeta med både traditionella och exotiska material.
Hans varv Scandi Yachts i finska Österbotten har byggt bl a havskappseglaren BIG FOOT och
Gotland Runt-vinnaren VISION.
Text: NISSE LUOMA
Den andra revolutionen när det gäller kompositmaterialens (blandade material, t ex
glasfiberarmerad plast) användning inom båtbyggnadsbranschen ja, inom industrin
överhuvudtaget - kunde man gott kalla det som nu sker och vi är, enligt många experters
bedömning, bara i början av den boomen ännu. Den första revolutionen på båtsidan
inträffade för ca tjugo år sedan när glasfiberarmerad plast (GRP = Glass Reinforced
Plastic) började användas för tillverkning av fritidsbåtar. I dag talar man om Fibre
Reinforced Plastic (FRP), eftersom det ofta är frågan om andra fibrer än glasfiber, en
aramidfiber som Kevlar t ex eller kolfiber.
Aluminium framförs av och till som ett material på kommande i båtskrov i ex. Man utgår
kanske från att det används inom flygindustrin, men faktum är att flygindustrin syns
vara i färd med att överge aluminiumet och man går alltmer över till kompositer. Då
handlar det förstås inte om glasfiberarmerad polyesterharts utan om S-glas,
kolfibermaterial, Kevlar och honeycomb i förening med epoxyharts.
Och det är där den modernaste teknologin inom one off-båtbygge har sina förebilder och
hämtar många av sina utvecklingsidéer.
Att ta efter flygindustrin är alltså på modet när det gäller havskappseglingens
formel-1-båtar, men billigt blir det inte och ofta krävs specialutrustning för att de
sofistikerade materialen skall kunna utnyttjas maximalt. Vad man däremot inte kan ta
efter när det gäller kompositerna är de dimensioneringsprinciper som gäller för
metaller. På Statens tekniska forskningsanstalt i Finland säger Gunnar Holm, som forskat
en hel del i kompositmaterialens egenskaper och hållfasthet, att man verkligen får myror
i huvudet av deras sätt att fungera tillsammans.
Och faktum är att ju mer man försöker ta reda på om dessa materials praktiska
användning, desto mer märker man att det finns mycket att lära. Det fungerar som med
all annan kunskap - ju mindre man vet desto enklare är det att dra slutsatser...
Utvecklingen är dessutom så snabb att risken finns att det man skriver ned i dag är
föråldrat i morgon.
En annan sak är att det finns många åsikter om vad som är bäst och vad som är det
riktiga, ibland baserade på kunskaper och egen erfarenhet, ibland kanske på fördomar
och ibland ligger det kommersiella intressen bakom. Att vaska fram guldkornen ur allt
detta är inte helt lätt.
Den här artikeln är inte tänkt som någon uttömmande beskrivning av kompositmaterialen
och deras egenskaper. Den vill försöka beskriva några grundläggande saker av vikt att
veta för den som praktiskt vill använda materialen. Om ni vill kan den också få
fungera som en bit konsumentupplysning, kanske ge blivande båtägare sådana
grundkunskaper att de kan ställa viktiga frågor när det gäller tillblivelsen av deras
nya båt.
För den som till vardags sysslar med one off-produktion av havskappseglare är siktet
hela tiden inställt på att bygga lätt och starkt och med fördelaktigast möjliga
viktfördelning i båten. Då kan man inte låta bli att snegla på de nya materialen och
teknikerna, men också den som skall ha en bruksbåt är betjänt av att känna till de
möjligheter som finns i dag.
Först en kort presentation av de mest använda materialen.
FIBRER
E-glas är den vanligaste och överlägset billigaste fibern. Det var just genom E-glas
som den första revolutionen inom båttillverkningen blev möjlig i början på
1960-talet. Man kunde med E-glas och relativt billig konstharts massproducera i form,
vilket öppnade nya vyer för båtindustrin och gjorde att träet som båtbyggnadsmaterial
slogs ut. Tillverkarna anammade snabbt den nya tekniken och snart översvämmades
marknaden av massproducerade fritidsbåtar i glasfiberarmerad plast - en utveckling på
både gott och ont, liksom all annan utveckling.
E-glas finns i många olika former - mattor i olika viktklass, tillverkade av huggen
fiber. Mattorna ger som sådana, utan förstärkning av rowing, knappast tillräcklig
styrka i förhållande till vikten. Utom mattorna finns det vävar av både garn och
ospunnen fiber, kallad rowing, och det finns vidare riktade material som är vävda i
olika förhållanden mellan varp och väft. Det finns 100-procentigt riktade material,
limmade eller sydda och kombinationer med matta/riktad rowing, hoplimmade eller hopsydda.
E-glasfibern tål "förädling" ganska dåligt enligt konstruktören Bruce
Kelly. Vad gäller garnvävar görs de dock av en klenare fibertyp som tål bearbetning
bättre. Vid masstillverkningen av olika slag av material behandlas den också rätt
ovarsamt och tar ytterligare skada. Regeln är att ju mindre bearbetad en fiber är, desto
starkare är den. Exempel: starkast är ett 100 procent riktat rowingmaterial som är
limmat eller sytt - svagast en väv av spunnet garn.
S-glas är tillverkat av en dyrare fiber av högre kvalitet och styrka jämfört med
E-glaset. Den utsätts inte för samma form av massproduktion och behandlas skonsammare
under tillverkningsprocessen. Bakom utvecklingen av S-glaset står amerikanska armén och
materialet används bl a inom flygindustrin. Till sin struktur är S-glasfibern jämfört
med E-glasfibern mycket tunnare, vilket ger större infästningsyta till hartsen. En
billigare typ används inom industrin. En fransk version av en ungefär likvärdig fiber
är R-glas, som också utvecklats inom flygindustrin och används bl a i rotorblad till
helikoptrar.
Kevlar är en annan känd fiber inom båtbranschen, dyrare än S-glaset och främst
karakteristiskt för sin utomordentliga draghållfasthet och sin motståndskraft mot
nötning. Kevlar är en aramidfiber, egentligen ett slags nylonmaterial. Den har, förutom
i båtar, en mycket vid användning, bl a i sportredskap, skottsäkra västar,
segelflygplan och t o m i segel har Kevlar använts, liksom i tågvirke. Kevlar tål sin
behandling och vävning. Kevlar har dålig tryckhållfasthet och kombineras därför med t
ex E-glas, S-glas och kolfiber för att ge starka laminat.
Till Kevlarns dåliga egenskaper räknas allmänt att den är svårarbetad. Med rätt
teknik är detta dock inte något problem. T ex trotsar Kevlar alla skärredskap om man
inte kan vässningstekniken.
Den dyraste av fibrerna är kolfibern, som egentligen är en ganska gammal fiber. Den är
tio gånger starkare än stål i förhållande till sin vikt. I motsats till Kevlar har
kolfibern bra tryckupptagningsförmåga. Den anses också lättarbetad.
Till dessa "rena" fibermaterial kommer olika slag av hybrider, d v s
kombinationer, t ex E-glas/Kevlar, Kevlar/S-glas, Kevlar/Kolfiber i olika förhållande
till varandra.
HARTSER
Vanlig polyester, båtplast kallad i dagligt tal, finns med olika egenskaper. I allmänhet
säljs de föraccelererade, antingen långsamt härdande eller snabbt härdande. De finns
också i s k miljöhartsformer med tillsats av en vaxlösning som under härdningen skall
hindra styrenavgång. Dessa hartser är i allmänhet ortoftalsyrabaserade, men det finns
också isoftalsyrabaserade, mera högvärdiga polyestertyper. Även dessa kan man köpa i
olika grad accelererade.
Vidare finns kemisk-resistenta hartser, t ex bisfenol och vinlyester, som är dyrare och
av bättre kvalitet och hållfasthet.
Epoxy är en annan högvärdig typ, men betydligt dyrare och svårhanterlig. Problem kan
uppstå vid användning av epoxy och polyester tillsammans. Polyestern fäster inte på
epoxy. Däremot går det bra med epoxy utanpå polyester.
DISTANSMATERIAL I SANDWICHKONSTRUKTIONER
Balsan, är ett träslag, alltså ett naturmaterial, är det billigaste distansmaterialet.
Det är också det äldsta sandwichmaterialet.
Numera finns moderna former av balsa, dyrare men också lättare som består av utvald
balsa. Balsa som distansmaterial ger styva laminat, men kräver ett omsorgsfullt arbete.
De ändställda träkuberna absorberar harts och fukt om en dålig infästning eller ett
dåligt laminat ger dem en chans till det.
Polyvinlyskumskivan, t ex Kegocell, är en typ av skumskiva med slutna celler. Den
absorberar inte harts eller vatten och finns i olika densitet, d v s olika grad av vikt
och hårdhet.
PVC-skumskivan (polyvinlyciorid) har också slutna celler. Den är mjukare än de tidigare
nämnda distansmaterialen och tål deformering bättre och är ett mera flexibelt
material. Exempel på PVC-skivor är airex och divinycell. Airex t ex tål komprimering
till halva tjockleken utan att deformeras. Också PVC-skivorna finns i olika densitet.
Honeycomb, typ honungskaka, är det senaste bland distansmaterialen.
Honeycomb har öppna celler rakt igenom skivan och finns med celler av olika utformning.
Vanligast är s k hexagonalcore med sexkantstruktur i cellerna. Ox-core och flex-core är
andra former. Honeycomb finns i aluminium och i aramidfiber fenollimmad och likaså i
olika densitet, d v s med olika väggtjocklek på cellerna och cellstorlek. Honeycomb
brukar också kallas aramidfiberpapper. Svårigheten när det gäller användningen av
honeycomb är att få en bra infästning utan att cellerna fylls med bindernedlet.
VAL AV MATERIAL
När man står inför val av material, d v s vilken typ av fiber, harts och
distansmaterial man skall använda är kanske den viktigaste utgångspunkten kostnaderna.
Prisskillnaderna är stora mellan de olika materialen och kombinationerna av dem.
Ibland blir det kanske yttre faktorer som påverkar valet, t ex materialets
tillgänglighet. Vissa material finns alltid på lager och kan levereras omedelbart eller
med kort varsel, medan andra bara tillverkas på beställning och finns inte på lager,
ens vid fabriken.
En minst lika viktig faktor som någonsin kostnad och tillgänglighet är naturligtvis
vilken typ av båt man planerar och vilket dess användningsområde kommer att vara. Om
det är en arbetsbåt eller en super-racer som skall byggas.
Betydelsefullt i sammanhanget är också byggarens erfarenheter och möjligheter. En del
av de nya materialen är erkänt svårbearbetade och kräver yrkeskunskap och erfarenhet,
ibland också specialutrustning.
I och för sig kan man gott säga att alla material är bra, om de används på rätt
sätt och på rätt plats. Det dyrbaraste och mest avancerade av material kan ge ett
totalt misslyckat resultat om det inte används ändamålsenligt och tvärtom kan en
billig kombination, rätt gjord, ge ett bra resultat. Vi har t ex hört talas om en
amatörbyggare i det båtbyggnadssakkunniga Österbotten. Han hade köpt Kevlar-duk i
Amerika och gjorde sig en båt av det. Han laminerade duken kant i kant, utan överlapp.
Vi har inte hört hur det gick sedan ...
Viktigt är att gå igenom det objekt som skall byggas och göra klart vilka egenskaper
som är önskvärda. Man bör också noggrant analysera för och nackdelar med materialen
och användningsområdena. Av stor betydelse är att man får klart för sig på vilket
sätt materialen kan kombineras på grund av sina egenskaper.
Detta gäller alltigenom: fiber kontra harts i alla laminat, fiber kontra fiber, speciellt
när det gäller single-skin (alltså enkelvägg, ej sandwich), och ytlaminat kontra
distansmaterial.
När man väljer en fiber med en viss hållfasthet, bör man söka ett bindemedel som
passar fibern och gör att fiberns hållfasthetsegenskaper kan tillvaratas på ett
optimalt sätt. Hartsens uppgift är att sprida påfrestningarna mellan fibrerna i
laminatet. Brister hartsen försämras eller upphör kraftöverföringen från fiber till
fiber och laminatet brister utan att man kunnat utnyttja fibern till fullo.
För att kunna utnyttja fiberns egenskaper bör hartsen därför ha åtminstone samma
brott-töjprocent (elongation) som fibern. Att i ett enkellaminat förstärka
konstruktionen med fibrer med annan brott-töjgräns än grundmaterialet behöver heller
inte ge önskat resultat. Vid överbelastning av ett flexibelt single-skin förstärkt med
ett stummare material når man kanske ingen förstärkningseffekt, utan risken är att man
överför belastningen på enbart den stumma förstärkningen tills den brister.
Ett bra resultat får man vid en kombination som går ut på att man t ex stöder olika
slag av påfrestningar med fiber med olika egenskaper, t ex stöder Kevlarns dåliga
tryckhållfasthet med E-glas eller S-glas, som båda är bättre på trycksidan än
Kevlarn, men på dragsidan har högre töj-brottprocent. Man räknar då med att Kevlarn
tar all dragpåkänning.
Viktigt är också att få det rätta förhållandet mellan 'skinnet' och
distansmaterialet i ett sandwichlaminat. Här gäller det igen att göra klart för sig
vilka egenskaper båten bör ha, vilket självfallet beror på användningen.
Skall båten vara flexibel och tåla stötar, typ bruksbåt eller cruiser, eller skall den
vara styv och lätt typ super-racer. Inte särskilt lyckad blir en kombination av ett
'skinn' i Kevlar eller kolfiber laminerat med epoxy och ett flexibelt PVC distansmaterial,
om man i viktbesparande syfte använder distansmaterial med för låg densitet. Med
tillräckligt hög densitet i distansmaterialet blir kanske viktbesparingen genom den
dyrbara fibern till stor del eliminerad.
Man kan tala om egenskaper i harmoni kontra egenskaper i disharmoni.
OPTIMERING TILL LÅGPRIS
Det allra effektivaste hindret för att använda alla de nya, sofistikerade
supermaterialen är väl plånboken och bankkontot. De kostar på tok för mycket. Man kan
kanske ändå göra en hel del utan att det kostar så mycket mer. Det finns nämligen,
enligt min mening, en hel del att göra - man kan kombinera ekonomiskt.
En erfaren dimensionerare av laminat, Ken Raybould på Martech i England har en kvalitets
och prismässig trappa som ser ut ungefär så här: Nederst E-glasmatta/vävd rowing och
vanlig polyester.
Nästa steg är att byta ut den vävda rowingen till en riktad.
Därefter byter man polyestern mot en högvärdigare harts, t ex vinylester. På följande
trappsteg har vi bytt ut E-glaset till riktat S-glas. Nästa steg är att blanda in Kevlar
och går vi ytterligare ett steg byter vi vinylestern mot epoxy. Överst på stegen tar
man i stället för S-glaset kolfiber tillsammans med Kevlar.
Vill man då till rimligt pris få ett bra resultat kan man stanna inom E-glassektorn, som
ju prismässigt ligger bra till och där det finns det allra bredaste sortimentet.
I enlighet med vad som sagts är det stor skillnad i kvalitet på den obearbetade
E-glasfibern och en tvinnad garnväv. Vill man ha en så hög kvalitet som möjligt
väljer man E-glas i enlighet därmed.
Genom att dessutom ta en högvärdigare harts, t ex vinylester, kan man nå värden som
ligger i närheten av de man uppnår med det betydligt dyrare S-glaset. Se figur 1.
En orsak till att värdena så radikalt kan förbättras är att man med vinylestern får
bättre kraftöverföring i laminatet än med den vanliga båtplasten, som har mindre än
hälften av glasets brott-töjprocent. Den vanliga hartsen brister alltså innan E-glasets
hållfasthet kommit i närheten av sin gräns. Den vanligaste båtpolyestern har en
brott-töjprocent under 2, medan vinylesterns ligger på 5.5, alltså strax över
E-glasets som är 4.8 procent. Se tabell.
Tester har visat att det redan vid låga töjprocenter, t o m under 1 procent, uppstår
sprickbildning i ett laminat, även om harts och glas var för sig har högre
brott-töjprocent. Det händer någonting som beror på att det i laminat alltid finns
tvärgående fibrer och det är möjligen detta som förorsakar krackeleringarna.
Hartsen spricker helt enkelt. Ju högvärdigare harts med högre brott-töjprocent desto
mindre är risken för dylika sprickor.
En väsentlig skillnad mellan E-glas och S-glas är att E-glaset har grövre trådar,
vilket minskar infästningsytan om man jämför med S-glas vars trådar är mycket fina.
En fördel till med vinylestern i sammandraget är dess större vidhäftningsförmåga som
förbättrar ett laminat med E-glas jämfört med motsvarande laminat med polyester.
Ett E-glasskinn kan naturligtvis kombineras med ett styvt distansmaterial eller ett
flexibelt, beroende på vilken användning båten skall ha och vilka egenskaper man vill
nå, t ex när det gäller styvhet, vikt o s v.
Utgångspunkten är att man väljer en sandwichkonstruktion, därför att man därigenom
får en båt som är lättare i förhållande till sin styvhet och styrka jämfört med
ett kompakt, enkelt laminat. Med en lättare båt får man bättre fartegenskaper. Man
klarar sig med mindre segel och motor och en lättare rigg eftersom dimensioneringen av
riggen står i förhållande till båtens vikt. Allt detta bidrar till att ge ett
billigare ekipage.
Väljer man ändå ett kompakt laminat har det stor betydelse hur fibrerna kombineras, så
att deras elasticitetsegenskaper harmonierar. I sandwich-laminatet gäller andra
principer.
Men, det finns också raciga högprisalternativ på kompositstegen. Om man alltså bortser
från kostnaderna och vill ha en styv och lätt super-racer med optimerad
viktkoncentration väljer man t ex så här:
För skinnet kan man i detta fall använda antingen kolfiber, som är dyrast, eller Kevlar
eller S-glas, som är billigast. Som distansmaterial honeycomb och som bindemedel
lämpligen epoxy, som har en betydligt högre limförmåga och ökar styvheten i
laminatet. Detta betyder att fibrernas goda egenskaper utnyttjas fullt. Epoxyns
brott-töjprocent är 5.5 och det värdet täcker alla tre fibermaterialen. S-glaset
ligger högst med 5.4 %, därefter kommer Kevlarn med 2.4 % medan kolfibern har lägsta
töjprocenten med 1.4.
Enligt principen med material i harmoni kunde man kanske dra slutsatsen att det inte är
meningsfullt att förstärka ett Kevlar-laminat med kolfiber - deras elasticitetsvärden
harmoniserar ju inte, men så enkelt fungerar det inte. Prov har nämligen visat att
materialen tillsammans - i ett färdigt laminat - får bättre egenskaper än vad deras
medeltal skulle förutsätta. Av detta kunde man då igen dra slutsatsen att en s k
hybrid, d v s en kombination av t ex Kevlar och kolfiber skulle vara det bästa, men så
enkelt är det inte heller. Bäst fungerar materialen som rena. Och ytterligare -
kombinerar man Kevlar med epoxy, behövs inte ens någon tryckförstärkning. Eventuellt
behöver man ett glaslager att slipa i, om man bygger på plugg.
Dock behöver det kanske betonas att man om man går till dessa ytterligheter - bör
anlita en kompetent och erfaren dimensionerare av laminaten. De kostar redan så mycket
att det säkert lönar sig.
Förresten tillkommer problem i användningstekniken när det gäller dessa högvärdiga
bindemedel. Det är ingen mening med att använda epoxy och laminera på vanligt sätt i
rumstemperatur. Under sådana betingelser får man inte på långa vägar ut epoxyns
värdefulla (och dyra) fördelar. Ett epoxy-laminat måste härda under rätt hög
temperatur, ca 80 grader.
Redan i och med att man väljer vinylester eller bisfenol i stället för vanlig orto-
eller iso-polyester måste man för att uppnå full hållfasthet efterhärda laminaten i
värme.
NYA METODER
När det gäller de nya materialen är utvecklingen oerhört snabb.
Tekniken att använda dem utvecklas också hela tiden.
I kombination med honeycomb som distansmaterial rekommenderas användning av s k prepreg
fiber, d v s fibermaterial som blötts maskinellt med katalyserad harts och levereras i
djupfryst form.
I stället för vanlig handlaminering använder man sig av vacuumbaggning, d v s laminatet
täcks med en lufttät duk och luften sugs bort under duken, som alltså smiter åt kring
laminatet. Härdningen av den frusna pre-preg-fibern sker i ugn.
Fördelen med pre-preg-metoden är att man får rätt mängd harts jämt fördelad och i
rätt förhållande härdare/harts när proceduren sker maskinellt. Den ibland opålitliga
mänskliga faktorn har därmed eliminerats.
Viktigt att komma ihåg i samband med användningen av de riktade materialen är att de
bör ha en så god sträckning som möjligt i den riktning man förutsätter att krafterna
verkar. När det gäller Kevlar tillkommer problemet att duken eller väven inte har
någon egen spänst och därför är svår att sträcka i en form eller på insidan av ett
skrov. Eventuellt kan vacuumbagging vara en utväg ur det dilemmat.
Att man faktiskt kan, med utnyttjande av det senaste i material och metod, nå avsevärda
viktbesparingar visar t ex Bruce Kellys halvtonnare Don Quixote IV som byggdes för
atenaren Ritsi Frances. Som distansmaterial i skrov och däck använde man honey-comb
-mellan skinn av pre-preg glasduk. Designern påstår att däck och skrovvikten blev bara
60 procent av ett konventionellt sandwichbygge men ändå med 50 procent högre
säkerhetsmarginal.
Genom viktbesparingen fick man en barlast procent på 70, naturligtvis med delvis
invändig barlast, och kunde göra en mycket tunn kölsektion. Med andra ord: vikten
koncentrerad till rätt ställe.
LITTERATUR BL A
Bruce Kelley: Building in Fibreglass; artikel i Yacht Racing/Cruising Magazine, september
1982; Tony Smith: Exotics and Ocean Racing, artikel i Seahorse, maj/juni 1982.
En uppfattning om prisskillnaderna mellan de
aktuella fibermaterialen ger en uppställning i Vetrotex Fiberworlds februarinummer.
Jämförelsen utgår från det 'vanliga' E-glaset. R-glas är jämförbar med S-glas.
E-glas 1
R-glas 5-9
Aramid (t ex Kevlar) 10-12
Kolfiber 30-50
|
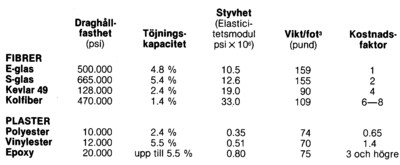
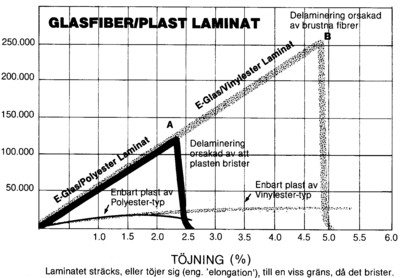
Figuren visar glas och harts i samverkan i typiska
belastningsdiagram för laminerad riktad E-glasfiber med en yttersta töjgräns på 250
000 psi. De undre kurvorna visar motsvarande värden för två hartser, polyester och
vinylester. Som synes förbättrar glaset avsevärt laminatets styrka i jämförelse med
hartsen, men gränsen går vid den maximala brott-töjgränsen hos hartsen. Om hartsen
brister innan fibern har nått sin yttersta styrka kan endast en del av fiberns
hållfasthet utnyttjas i förstärkningen av laminatet.
Punkt A i diagrammet visar den yttersta sträckgränsen hos en fiber som laminerats med
polyesterharts. Punkt B visar den yttersta hållfastheten hos samma fiber, laminerad med
en högvärdig harts, t ex vinylester som når en högre brott-töjprocent utan att
brista.
Det här gäller laboratorieförsök med riktade fibrer. Vävda material når bara
hälften av denna styrka på grund av att endast hälften av materialet är med och tar
upp belastningen. Mattorna utvecklar endast en tredjedelavstyrkan hos ett riktat material
eftersom fibrerna är slumpvis ställda och bara en tredjedel av fibrerna är i sådan
position att de tar upp belastning.
Det slags E-glas som används av båtbyggare är inte så starkt som ett laboratorieprov
beroende på den massproduktionsprocess som fibrerna genomgått. Siffrorna som följer ger
ett teoretiskt optimum vid ett omsorgsfullt arbete i ett båtbygge - ett slarvigt bygge
kan ge betydligt lägre styrka:
Drag (psi) Tryck (psi)
Riktade fibrer 113 800 49 800
Vävda fibrer 32 700 17 000
Matta 11 400 17 000
|
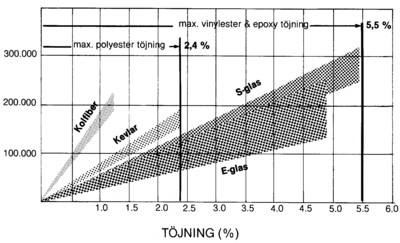
Diagrammet visar styrka och sträckning hos olika fibrer
och hartser. Diagrammet gäller laminat av riktade, högvärdiga råfibrer, d v s sådana
som är helt obehandlade. Glas/harts-förhållandet är 50-50. Triangeln för varje fiber
visar ett område, där den övre linjen ger hållfastheten hos ett laminat gjort i
laboratorium av försiktigt behandlade fibrer och den undre linjen representerar bästa
möjliga hållfasthet uppnådd genom användning av massproducerade fibermaterial i ett
laminat gjort på ett båtvarv.
Som synes utvecklar kolfibern sin maximala styrka långt innan polyesterhartsens
maximumtöjgräns har uppnåtts. För ren töjpåkänning skulle polyester vara perfekt i
kombination med kolfiber. Kevlar når sin maximala styrka vid samma gräns som polyesterns
när det gäller töjning och teoretiskt skulle det inte vara några fördelar med att
använda någon annan harts. I realiteten är dock vinylester att föredra eftersom ett
litet fel på polyesterhartsen kan leda till en bristning i ett tidigt skede. E-glasets
och S-glasets hållfasthet ökar märkbart om man använder vinylester, vilket framgår av
diagrammet.
|