Learning From The Past
- Fremantle
Moves Ahead
By
Matt Hanson
The Fremantle 505 has been developed over the last three years by co-operation between a number of long-term West Australian 505 devotees and Brett Burvill of Windrush Yachts.
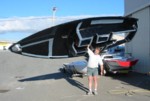 |
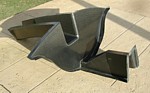 |
Why bother with making yet another set of moulds in Australia? What is wrong with existing designs? What extra expertise can be brought to bear on such a well established and well thought-out craft? I hope to give some insight in to all this and to offer up our interpretation of the 505.
In Western Australia we sail in tough conditions. Strong sea breezes of 20-30 knots and choppy open water off Fremantle means the boats sustain a lot of wear and strain. The new long luffed kite, as well as the trend toward high aspect foils has increased the loads sustained by the rig and hull and particularly by the centercase. The demanding conditions also require that the ergonomics of the internal layout of the boat must be optimal to allow the skipper and crew to get round the course and make rig adjustments as easily and as quickly as possible. These conditions are fantastic for ocean dinghy racing as many of you will discover in December 2002.
When I started sailing 505s 15 years ago nearly all the boats in Australia were Kyrwoods. These were simple but sturdy and easy to rig. The Aussies were dominant and the Kyrwood brothers themselves were a substantial part of the reason for that prowess. I have owned 3 Kyrwoods over the years and initially thought that there was little that could be improved on. Certainly the end grain balsa floors have remained stiff and secure over that time despite our tough conditions. There were, however, problems with flexibility of the side tanks and case, which tended to break free of the
for'ard thwart and compress under load. As we departed from the floppy rig to the higher tensions now used the problems became more pronounced. The side tanks are also prone to splitting from the hull due to a poor bond. The later Kyrwoods used better layups but the fundamentals of the design remained the same.
Kyrwood no longer makes 505s but in their wake has come three other Australian manufacturers before us with modifications and improvements in layup and layout. I was most impressed with the improvements that the Van Munsters made particularly in the internal layout and support of the centercase as well as hull shape and have owned two of these craft. The ergonomics of the Van Munster cockpit made sailing the boat easier and definitely gave the boat a more modern look, though fitting out the hull was more difficult. The mast step was a weak point and needed modification to tolerate the compressive loads and lateral forces and the use of foam in the floor made the hull much more prone to denting from impact with jinkers, kneecaps and trapeze
hooks. In the meantime we had a chance to look at the overseas manufacturers offerings at world championships we attended.
The longevity of the Waterats was astonishing, clearly the Nomex Honeycomb/epoxy layup was more durable than anything else. Further enquiry indicated that these materials were difficult to use well and Australian manufacturers of 505s at that time were understandably cautious about trying. We needed to have a builder with plenty of experience with epoxy layups-preferably pre-preg carbon composites that had the best strength and stiffness to weight ratio. The Rondars
had improved on the spinnaker chute design thereby lowering the friction in the system and using the chute itself to stiffen the foredeck. We saw great ideas on other designs (Maders and Duvoisins) and were left with the thought that we could adopt and adapt the best features of all these to create something new and hopefully better.
The principles we adopted in developing the new Fremantle 505 were generated from this history and include the following:
-
Optimal hull shape. Continuing the trend set by the latest Van Munster hulls with finer entry, more chine and flatter aft sections
-
Improve the engineering of the supports of the hull decks and casing by
-
Minimising the number and extent of
joins between the components. All joins are potential points of weakness. By reducing the hull, decks, case cap, thwarts, bulkheads maststep chute and transom to just 3 interlocking moulded components the potential for failure at
joins is minimised. Furthermore, the moulds themselves interlock precisely guaranteeing precise alignment of the components. Fewer joins also mean less adhesive and quicker build times therefore less weight and lower labour cost.
-
Triangulating the
for'ard thwart to lock the principal load bearing part of the case cap to the floor as well as supporting the compression loads from the side tank. A similar arrangement to the latest 470s.
-
Triangulating the mast step by converting it to a flat topped hollow pyramid. The sidewalls of the mast step share the vertical compression loads and dissipate them over a broad area of the hull. They also resist the lateral forces far more effectively than a single vertical strut and as they lock inside the aft bulkhead they are both further supported and not dependent on the join for stability.
-
Triangulating the support for the case cap at the aft end of the case to resist the lateral loads of the mainsheet on the case. The aft thwart also is a moulded component continuous with the casecap and sidetank (one piece - no joins). It runs low and is attached to the floor thereby stiffening it in a similar fashion to the aft thwart on the Van Munster but without the need for a join at the sidetank.
-
Using the moulded
for'ard bulkhead and chute as structural supports for the foredeck and to resist compression loads from the rig on the hull. The monocoque concept.
-
The transom meets the trailing edge of the hull at a cleanly moulded seam without intervening core material giving a cleaner sharper and harder edge with less risk of water seepage into the core.
-
Shifting the opening of the centercase through the hull to take better account of where the leading edge of the board is located and to facilitate use of the latest high aspect foils.
-
Longitudinal bulkheads between hull and sidetanks further reinforce the structure creating an 'internal honeycomb' effect. This greatly adds to the rigidity of the sidetank and hull around the area of maximum compression from the sidestays and maximum impact from the crew.
-
Using the latest and best materials. We are fortunate to have boat builder Brett Burvill and his company Windrush Yachts who have extensive experience in the construction of a variety of high performance dinghies including International Moths,
14s, Cherubs, lightweight Sharpies, Javelins, as well as high performance super catamarans such as the hydrofoil "Spitfire". Brett is both very experienced and comfortable with working with pre-preg epoxy layups with Nomex as well as the more conventional materials. One of his craftsmen
had just returned from working with the McLaren
F1 racing team where the "dark arts" of using this material are at the most advanced stages of development and refinement. Pre-preg layups are not without technical difficulties including such things as porosity and therefore potential water uptake into the core plus distortion in the mould if the correct tooling is not used. Windrush
had used over 800kg of the material (enough for nearly 20 505s!) in the year prior to our first pre-preg hull.
-
Careful reinforcement of load areas. In both the prepreg and vinyl ester/carbon layups a lot of thought has gone into reinforcernent of specific areas by increasing skin thickness and careful use of different types/weaves of cloth. As well as the areas subject to rig tension and foil loadings there are other sites where impact loads are high and frequent such as tank tops and cockpit floor.
-
The conventional carbon/vinyl ester boats have 10mm end grain balsa in the floors which has much better impact resistance than foam. (The Kyrwoods had 6mm balsa). Divinycell�
foam is used in the decks of these boats in non-impact areas. High-density foam or marine ply is used as a core material at fitting attachment points in the conventional layup boats. In the pre-preg epoxy boats Nomex honeycomb core material is used everywhere except the mast step and case cap.
-
The low aft thwart and down sloping
for'ard thwart open up the cockpit making crew movements easier and the cockpit less cluttered. The angle and position of the front thwart is ideal for cleating and releasing the jib from the wire without interfering with the plate.
-
The Rondar-like chute entry, which has been further widened to ease handling of the new kites, has greatly reduced the friction in the system and therefore wear and tear of both the crew and kite!
-
The hollow pyramid mast step has an open aft end that lines up with the sides of the centercase giving a continuous cavity along the centerline from the
for'ard bulkhead to the aft end of the case. This opens up all sorts of possibilities for rigging control systems and elastic takeups.
-
The hollow aft thwart can be used as a conduit for control lines to the side tanks
-
A simple removable aluminium plate serves as a mounting for turning blocks at the side of the casing at the level of the aft thwart. It is locked in position by its shape (which forms a key-lock with the inside of the aft thwart and a single bolt rising up from the floor. It, and all its associated blocks and lines can be released and removed in less than a minute and replaced just as easily.
-
A new forestay tang has been designed to facilitate tensioning of the forestay from below or fitting a furler if required.
-
A moulded rebate in the foredeck for the standard Z-spar mast ram fitting that locates and stabilizes the fitting precisely.
-
Other fit-out options are available.
SUMMARY
As most Aussies know the Australian dollar has been plummeting in value from virtual parity with the US dollar 20 years ago to only 54 cents today. This means our exports are cheap, as labour costs are relatively low in US dollar terms despite similar technology and educational levels. We are a cheap and very safe place to visit and are nuts about watersports. All this adds up to the fact that Australia is a great place to build, use and export boats. Which is probably why we have four active 5 0 5 builders. The other guys make great boats too.
The Fremantle 505 has resulted directly from the enthusiasm and interest of fanatical 505 enthusiasts combined with the efforts of expert boatbuilder and dinghy sailor, Brett Burvill. Five boats have now been completed including two pre-preg hulls and a 3rd pre-preg boat is under construction with another to follow. We have
had advice and input from various other sources including the "By Design" engineering/naval architect group. Most importantly this boat is a distillation of what we believe to be the best ideas of all the other manufacturers of 505s plus many other high performance dinghies both in Australia and overseas. No doubt someone will improve on these ideas, we certainly plan to.
TANK TALK - FALL 2002
|